“Predictive maintenance isn’t just about saving money; it’s about planting the seeds for growth.”
Klaus Blache, Reliability & Maintainability Center at the University of Tennessee
In the industrial sector, managing the lifecycle of assets is critical to ensuring operational efficiency and longevity. Predictive maintenance, powered by artificial intelligence (AI), is revolutionizing the way businesses manage and maintain their equipment, leading to prolonged asset life and reduced costs. This article delves into how predictive maintenance AI is being implemented to transform asset lifecycle management, supported by industry data and practical applications.
Significance of Predictive Maintenance in Asset Lifecycle Management
The traditional approach to maintenance—either preventative maintenance based on scheduled intervals or reactive maintenance after failures occur—often leads to either unnecessary maintenance costs or expensive downtime and repairs. Predictive maintenance AI offers a more efficient solution by predicting equipment failures before they happen, allowing for timely intervention.
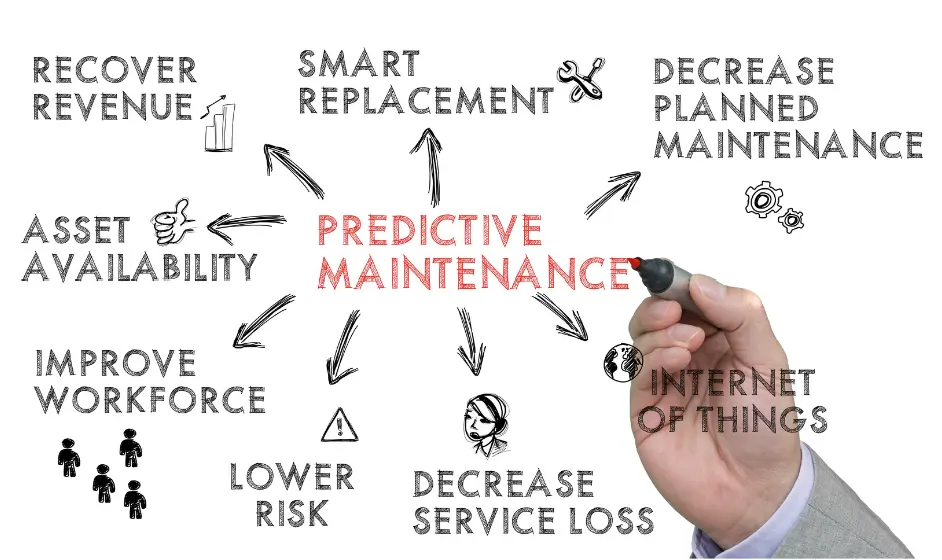
Industry Insights:
- According to a report by PwC, predictive maintenance can reduce costs by 12%, improve uptime by 9%, and extend the lives of machines by 20%.
- MarketsandMarkets forecasts the global predictive maintenance market to reach $12.3 billion by 2025, up from $4.0 billion in 2020, at a CAGR of 25.2%.
Real-World Application:
- Siemens has integrated AI into its predictive maintenance systems for trains and tracks, using sensors and data analytics to predict wear and tear. This approach has notably reduced train delays and maintenance costs, significantly improving service reliability and customer satisfaction.
Enhancing Asset Lifecycle Management Through Predictive Maintenance AI
Optimal Maintenance Scheduling: Predictive maintenance AI uses data from sensors and historical performance to accurately forecast when maintenance should be performed. This optimizes maintenance schedules, ensuring that maintenance is only done when necessary and not according to a less efficient calendar-based schedule.
Extended Asset Lifespan: By maintaining equipment just at the right time, predictive maintenance helps avoid excessive wear and tear that can shorten an asset’s lifespan. This not only ensures that machinery runs more efficiently but also delays the need for costly replacements.
Cost Reduction and Resource Allocation: Predictive maintenance allows companies to allocate resources more effectively, prioritizing maintenance activities that are truly necessary. This strategic approach reduces the waste of resources and focuses efforts where they can generate the greatest return on investment.
Challenges in Implementing Predictive Maintenance AI
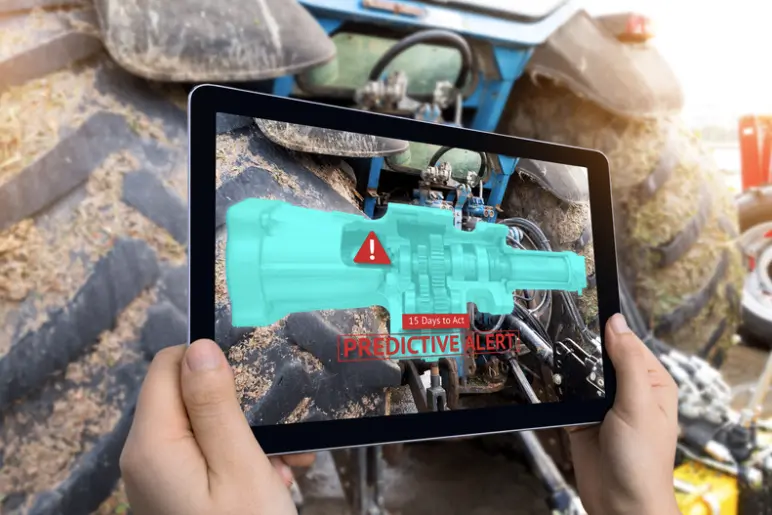
Integration with Existing Systems: Integrating AI-driven predictive maintenance systems into existing industrial infrastructures can be challenging. It requires compatibility with existing machinery and data systems, which may involve significant upfront costs and technical adjustments.
Data Management and Quality: Effective predictive maintenance depends on high-quality data. Collecting, storing, and processing large volumes of data from industrial sensors can be daunting, requiring robust data management systems and processes.
Skilled Workforce: Implementing and managing AI-based predictive maintenance systems require a workforce skilled in both the operational aspects of the industry and data analytics. The lack of such skills can be a significant barrier to effective implementation.
PeakMet’s Role in Revolutionizing Asset Lifecycle Management
Advanced Predictive Maintenance Solutions: PeakMet offers cutting-edge predictive maintenance solutions tailored for specific industry needs. These solutions integrate seamlessly with existing hardware and software, providing accurate predictions and actionable insights.
Continuous Improvement and Analytics: PeakMet’s systems are designed for continuous learning, improving their accuracy and effectiveness as more data becomes available. This adaptive capability ensures that predictive maintenance recommendations become more precise over time.
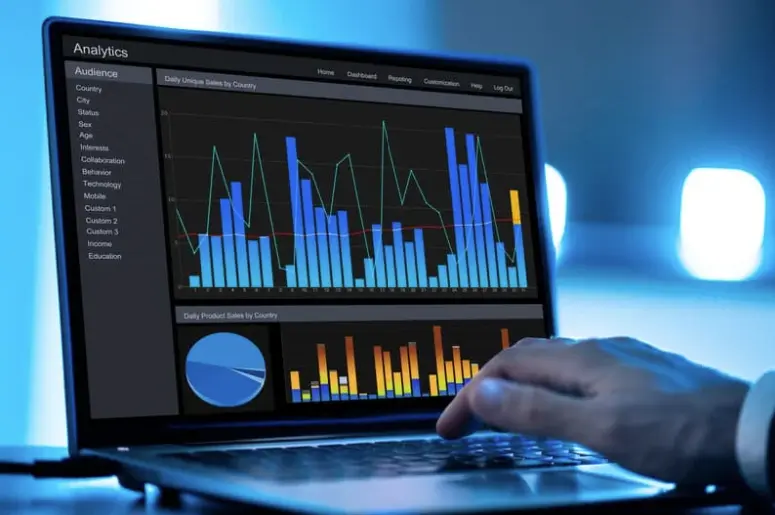
Training and Support: Understanding the complexities of predictive maintenance AI, PeakMet provides comprehensive training and support to ensure businesses can effectively deploy and utilize these advanced systems. This support helps companies overcome the skills gap and maximize the benefits of AI-driven maintenance.
In conclusion, predictive maintenance AI is a game-changer in managing the lifecycle of industrial assets. By enabling more precise maintenance interventions, AI not only extends the lifespan of equipment but also drives down operational costs, thereby enhancing overall business growth and sustainability. With solutions like those from PeakMet, industries are well-equipped to transition to smarter, more efficient maintenance practices that can significantly impact their bottom line.