“Efficiency in manufacturing revolves around minimizing downtime and maximizing production.”
Henry Ford
Downtime in manufacturing can lead to significant revenue loss, reduced productivity, and increased operational costs. Predictive analytics tools are increasingly employed to preemptively identify potential equipment failures and schedule maintenance, thereby minimizing unexpected downtime. This article explores how predictive analytics is revolutionizing maintenance strategies in the manufacturing sector, supported by industry data and highlighting the effective deployment of these tools.
The Impact of Downtime in Manufacturing
Unplanned downtime in manufacturing is a costly issue, impacting not just the immediate production line but also the broader supply chain and customer satisfaction levels. The ability to predict and prevent equipment failures is therefore a crucial competitive advantage.
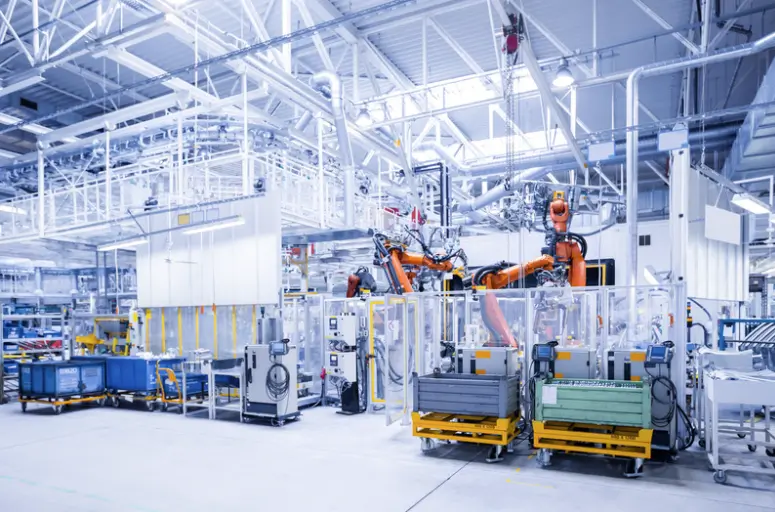
Industry Insights:
- According to a study by Deloitte, manufacturing industries experience an average of 800 hours of downtime annually, which can cost companies up to $22,000 per minute depending on the industry sector.
- Research from Aberdeen Group reveals that unplanned downtime can reduce production capacity by 20% and is one of the biggest challenges facing manufacturers today.
Real-World Application:
- Companies like General Electric have integrated predictive analytics into their manufacturing operations. GE’s Predix platform uses sensors and machine learning to predict equipment failures before they occur, significantly reducing downtime and maintenance costs.
How Predictive Analytics Tools Optimize Manufacturing Maintenance
Predictive Maintenance: Predictive analytics tools utilize machine learning algorithms and historical data to predict when a machine is likely to fail or require maintenance. This approach allows manufacturers to move beyond routine or reactive maintenance strategies to a more efficient, condition-based maintenance plan.
Enhanced Resource Allocation: By predicting when and where maintenance will be required, companies can better allocate resources, including labor and replacement parts. This strategic planning helps avoid both over-maintenance and catastrophic machine failures, optimizing operational costs and extending the lifespan of machinery.
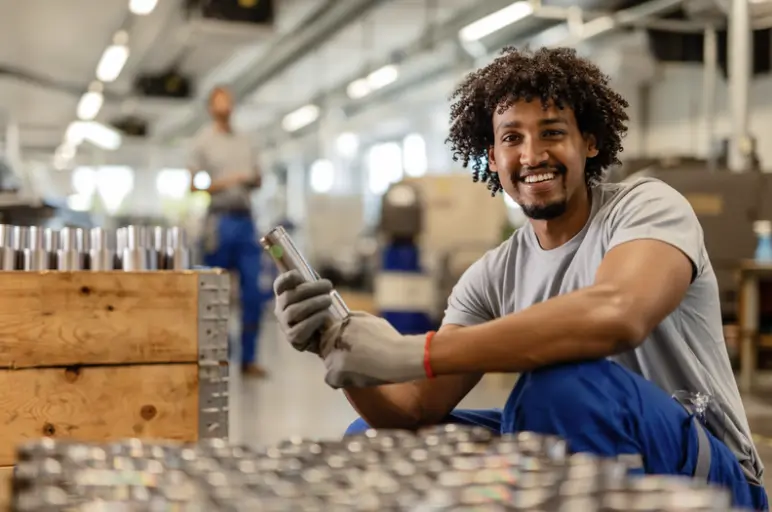
Improved Production Scheduling: Predictive analytics also aids in refining production schedules by incorporating maintenance predictions. This ensures that downtime for maintenance has minimal impact on production deadlines and order fulfillment.
Challenges and Solutions in Implementing Predictive Analytics for Maintenance
Integration with Existing Systems: Integrating predictive analytics tools with existing manufacturing systems can be challenging. These systems must not only be compatible with older machines but also capable of integrating data from various sources to provide accurate predictions.
Data Quality and Access: The effectiveness of predictive analytics depends heavily on the quality and completeness of the data collected. Ensuring that sensors are properly installed and maintained and that data is accurately collected and processed is critical.
Skilled Personnel: While predictive analytics tools automate many aspects of maintenance planning, skilled personnel are required to manage these tools and make informed decisions based on their outputs. Training for existing staff and hiring new personnel with data analytics expertise is often necessary.
PeakMet’s Role in Enhancing Manufacturing Efficiency
Advanced Predictive Analytics Platforms: PeakMet offers advanced predictive analytics platforms that are customized for the manufacturing sector. These platforms are designed to seamlessly integrate with existing machinery and IT systems, providing real-time insights and predictive alerts.
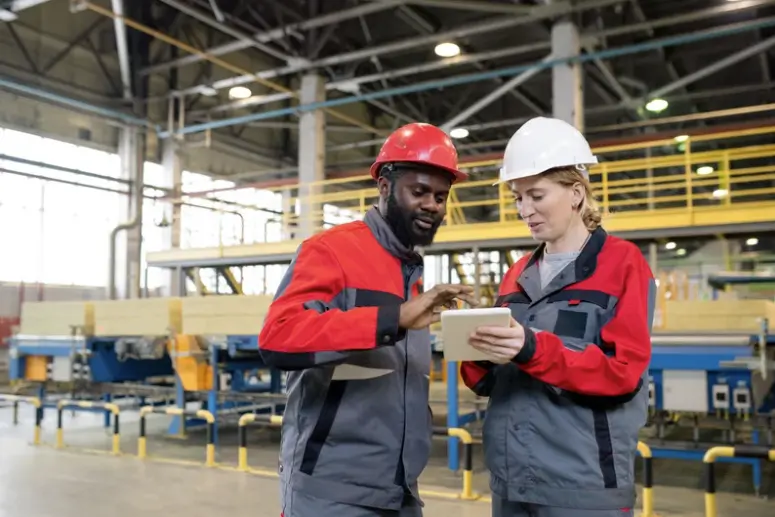
Continuous System Improvement: PeakMet ensures that its analytics tools are continuously refined based on user feedback and new data, enhancing their accuracy and reliability over time.
Expert Support and Training: Understanding the complexities of deploying predictive analytics in manufacturing, PeakMet provides expert support and training to ensure that companies can fully leverage the benefits of predictive maintenance.
In conclusion, as manufacturers seek to minimize downtime and optimize production, predictive analytics tools present a powerful solution. By forecasting equipment failures and maintenance needs, these tools enable manufacturers to plan proactively, ensuring continuous production and operational efficiency. With the implementation of predictive analytics solutions like those provided by PeakMet, companies can not only reduce downtime but also enhance overall productivity and profitability.